In the intricate web of supply chain logistics, the seamless movement of goods from warehouse to destination has become a critical factor in customer satisfaction. As consumer expectations soar and delivery timelines tighten, the role of the Warehouse Transportation Management System (TMS) has evolved from a mere logistical tool to a pivotal element in ensuring customer contentment.
Understanding Warehouse Transportation Management System
Warehouse Transportation Management Systems are sophisticated software solutions designed to orchestrate the transportation aspects of supply chain operations within a warehouse. These systems go beyond traditional inventory management, offering a comprehensive approach to planning, executing, and optimizing the movement of goods.
A robust TMS facilitates a range of activities, including route optimization, carrier selection, and freight auditing. The overarching goal is to enhance efficiency, reduce costs, and, most importantly, meet customer expectations through timely and accurate deliveries.
Streamlining Operations Through TMS
1. Product Planning and Control
One of the key functionalities of a Transportation Management System in a warehouse setting is product planning and control. Warehouses deal with a multitude of products, each having its own specific transportation requirements. A Transportation Management System aids in creating an organized plan for the transportation of these products, taking into account factors such as weight, size, and destination.
By efficiently managing the product planning and control process, a Transportation Management System ensures that the right products are transported to the right locations at the right time. This not only minimizes errors but also contributes to a more streamlined and efficient warehouse operation.
2. Supply Chain Logistics
The integration of a Transportation Management System goes beyond the confines of individual warehouses; it extends to the entire supply chain. In the realm of supply chain logistics, TMS plays a central role in optimizing the movement of goods from suppliers to manufacturers, and finally to the end customer. The software provides real-time visibility into the transportation process, allowing for better decision-making and problem-solving.
A well-implemented TMS in the supply chain logistics framework results in enhanced coordination and collaboration among various stakeholders. This, in turn, leads to reduced lead times, lower costs, and an overall improvement in the efficiency of the entire supply chain.
Demand Planning in Supply Chain Management
Customer satisfaction hinges on the ability of businesses to meet demands accurately and promptly. This is where demand planning in supply chain management becomes instrumental. Transportation Management Systems, when seamlessly integrated into the supply chain, assist in predicting demand patterns based on historical data, market trends, and other relevant factors.
Using advanced algorithms and analytics, TMS aids in forecasting product demand with a high degree of accuracy. This ensures that warehouses are well-prepared to fulfill customer demands, minimizing stockouts, optimizing inventory levels, and ultimately improving customer satisfaction.
The Direct Impact on Customer Satisfaction
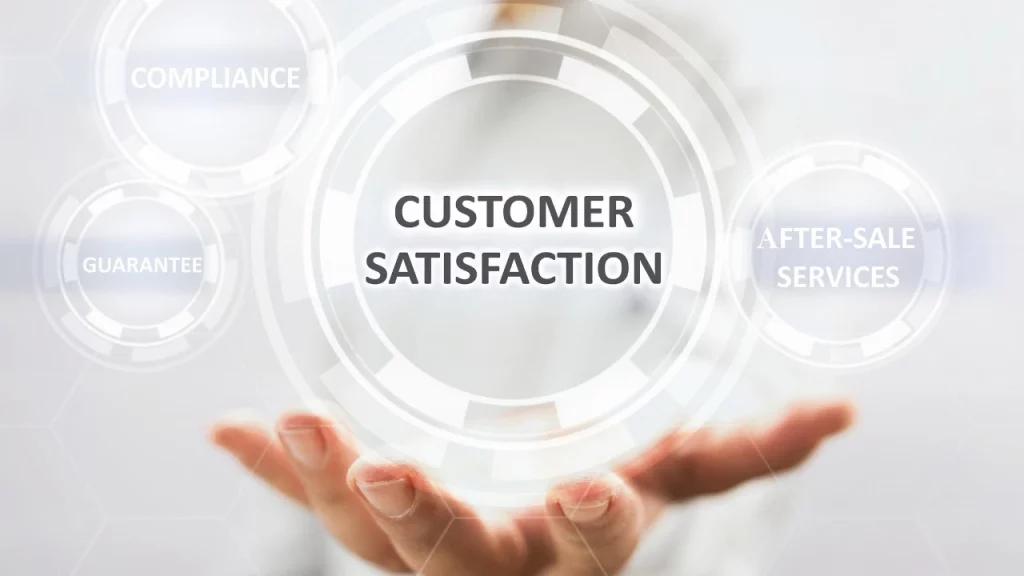
1. Timely Deliveries
One of the most direct and tangible impacts of an effective Transportation Management System on customer satisfaction is through timely deliveries. By optimizing route planning, selecting the most efficient carriers, and monitoring the transportation process in real-time, a TMS ensures that customers receive their orders promptly. Timely deliveries not only meet customer expectations but also contribute significantly to overall satisfaction.
2. Cost Reduction
Efficient transportation management directly translates to reduced costs. Transportation Management Systems achieves this by optimizing routes, consolidating shipments, and minimizing transportation-related errors. The resulting cost savings can be passed on to customers in the form of competitive pricing, further enhancing their satisfaction and loyalty.
3. Enhanced Visibility
Customers value transparency in the supply chain process. Transportation Management Systems provides enhanced visibility by offering real-time tracking and monitoring of shipments. This transparency not only instills confidence in customers but also empowers them to plan and manage their operations more effectively, knowing exactly when to expect deliveries.
4. Improved Communication
Efficient transportation management directly translates to reduced costs. Transportation Management Systems achieves this by optimizing routes, consolidating shipmEffective communication is a cornerstone of customer satisfaction. A Transportation Management System facilitates improved communication by enabling warehouses to provide proactive updates on the status of orders. Whether it’s an update on shipment progress or a notification about potential delays, timely and accurate communication builds trust and loyalty.ents, and minimizing transportation-related errors. The resulting cost savings can be passed on to customers in the form of competitive pricing, further enhancing their satisfaction and loyalty.
The Impact on Customer Satisfaction
The ultimate goal of any supply chain operation is to satisfy customer expectations efficiently. The role of a TMS in achieving this goal is profound. Let’s delve into the ways in which TMS directly impacts and enhances customer satisfaction.
1. Timely Deliveries
With a robust TMS in place, warehouses can ensure timely deliveries of products. The software optimizes route planning, selects the most efficient carriers, and monitors the entire transportation process in real-time. As a result, customers receive their orders promptly, contributing significantly to overall satisfaction.
2. Reduced Costs
Efficient transportation management directly translates to reduced costs. By optimizing routes, consolidating shipments, and minimizing transportation-related errors, a TMS helps in cutting down operational expenses. These cost savings can be passed on to customers in the form of competitive pricing, further enhancing their satisfaction.
3. Enhanced Visibility
Customers appreciate transparency in the supply chain process. A TMS provides enhanced visibility by offering real-time tracking and monitoring of shipments. This transparency instills confidence in customers and allows them to plan and manage their operations more effectively, knowing exactly when to expect deliveries.
4. Improved Customer Communication
Effective communication is a key element of customer satisfaction. A Transportation Management System enables warehouses to communicate proactively with customers regarding the status of their orders. Whether it’s an update on shipment progress or a notification about potential delays, timely and accurate communication builds trust and loyalty.
Conclusion
In conclusion, the integration of a Transportation Management System into warehouse operations is not just a technological upgrade; it’s a strategic move toward achieving higher levels of customer satisfaction. From optimizing product planning and control to streamlining supply chain logistics and enabling accurate demand planning, a TMS serves as a linchpin in the modern-day warehouse ecosystem.
As customer expectations continue to evolve, businesses must embrace technological solutions like Transportation Management Systems to stay ahead in the competitive landscape. By prioritizing timely deliveries, reducing costs, providing enhanced visibility, and improving communication, warehouses can create a customer-centric supply chain that sets them apart in the market.
In essence, the synergy between Transportation Management Systems and customer satisfaction is not just a connection—it’s a competitive advantage that propels businesses toward sustained success.