One of the most impactful ways to achieve this excellence is through the implementation of an efficient Warehouse Management System (WMS), which plays a crucial role in improving in-plant logistics. As companies evolve, so do their logistics operations, and the need for real-time inventory management, streamlined workflows, and seamless communication between departments has never been greater.
SKUBIQ’s offers a comprehensive solution for businesses looking to elevate their logistics performance. This article explores the key benefits of adopting SKUBIQ’s and how it drives operational excellence in in-plant logistics.
What is SKUBIQ's SaaS WMS?
SKUBIQ is a state-of-the-art, cloud-based WMS that uses real-time data to optimize warehouse operations. SKUBIQ’s model makes it an attractive choice for businesses seeking to improve operational efficiency without heavy upfront costs or complex infrastructure. With features like advanced inventory management, intuitive user interfaces, automated workflows, and scalability, it is designed to enhance the speed, accuracy, and flexibility of warehouse and logistics operations.
SKUBIQ’s provides the ability to access and manage your warehouse data from anywhere, enabling better control and visibility of your logistics processes in real-time. Whether you’re managing a single facility or a network of warehouses, SKUBIQ’s offers the flexibility and adaptability that modern logistics operations require.
Key Benefits of SKUBIQ's in In-Plant Logistics
1. Streamlined Workflow and Operational Efficiency
In any plant, efficiency is key to achieving high operational performance. SKUBIQ’s offers several tools designed to automate and streamline workflows. From order picking and packing to inventory management and shipping, each process is optimized to reduce bottlenecks and increase throughput. The system ensures that warehouse staff follow the most efficient paths, reducing manual errors and improving order accuracy.
By implementing real-time data exchange and providing a central hub for all logistics-related operations, SKUBIQ allows for a seamless flow of information. As a result, plants can quickly adapt to changing conditions, making smarter decisions that drive higher productivity.
2. Real-Time Visibility and Control
One of the significant challenges in traditional warehouse systems is the lack of real-time visibility into inventory and operations. SKUBIQ’s provides detailed, up-to-date insights into stock levels, order statuses, and the flow of goods throughout the facility. This real-time visibility ensures that every department involved in logistics – from shipping to receiving to inventory control – can track operations as they happen, allowing for immediate corrective actions if necessary.
Real-time data also enhances the ability to forecast demand, plan inventory levels more accurately, and improve decision-making regarding restocking, product distribution, and order fulfillment.
3. Scalability to Support Growth
As businesses grow, so do the demands on their warehouse operations. SKUBIQ’s offers scalability, meaning it can easily adapt to the expanding needs of an enterprise. Whether your company operates in a single location or across multiple sites, the system scales efficiently without the need for additional hardware or extensive IT support.
The system also integrates with other business management tools, such as Enterprise Resource Planning (ERP) and Transportation Management Systems (TMS), to ensure the flow of data remains uninterrupted as your logistics operations expand.
The integration capabilities of SKUBIQ include:
- Streamlined workflows, reducing the need for manual data entry and errors.
- Unified data management, ensuring that all stakeholders have access to the same accurate and up-to-date information.
- Enhanced operational efficiency, enabling faster decision-making and reducing delays in the supply chain.
4. Improved Inventory Management and Accuracy
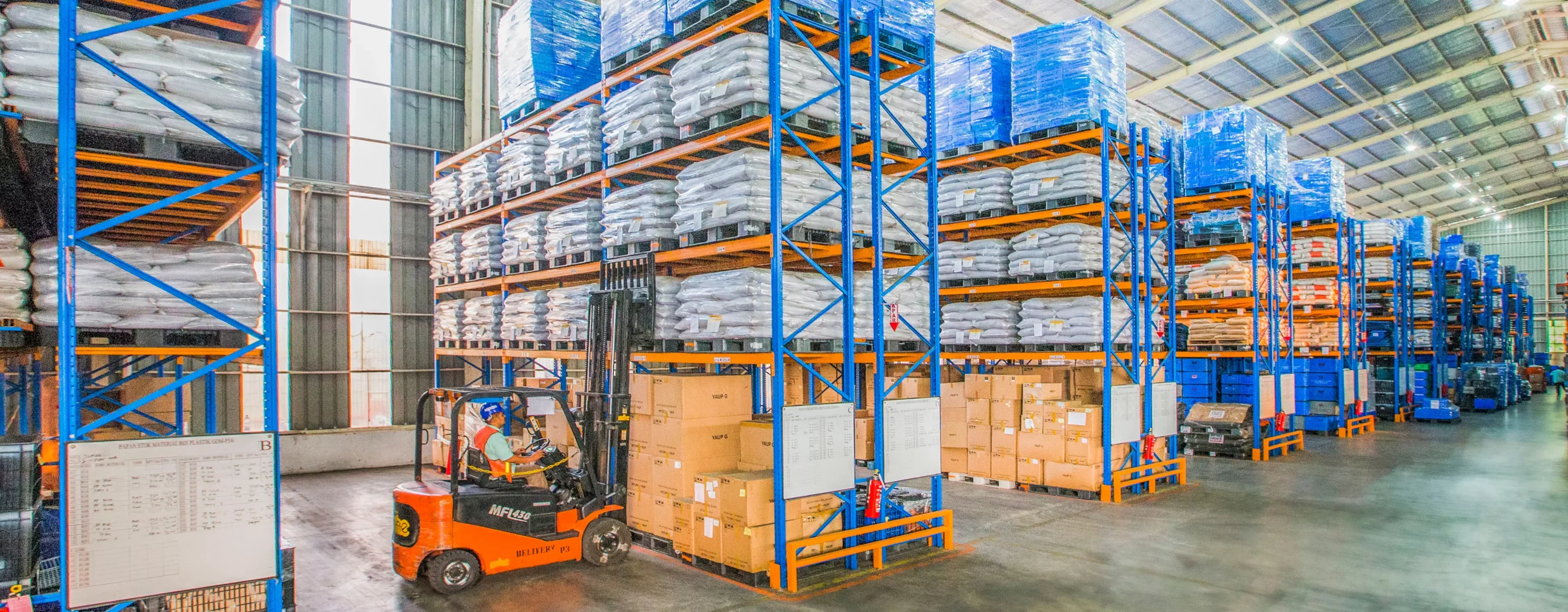
Effective inventory management is at the heart of operational excellence in in-plant logistics. SKUBIQ’s offers powerful inventory tracking capabilities, ensuring that every product is accounted for in real-time. With automated stock audits, businesses can reduce the risk of overstocking or stockouts, resulting in better resource allocation and optimized order fulfillment.
By integrating with barcode scanning and RFID technology, SKUBIQ allows for automatic inventory updates, ensuring that data is always accurate and up-to-date. This leads to fewer errors, better product traceability, and a significant reduction in manual inventory checks.
5. Enhanced Labor Management and Productivity
Labor costs are a significant part of any logistics operation. With SKUBIQ’s advanced labor management tools, businesses can optimize workforce allocation based on demand and task priority. The system can suggest the most efficient routes for workers to follow, reducing downtime and increasing the number of tasks completed per hour.
By providing real-time feedback on labor performance, SKUBIQ allows managers to assess worker productivity and make adjustments as needed. This level of detailed tracking not only improves employee accountability but also drives greater operational output and cost-effectiveness.
6. Seamless Integration with Other Systems
System integration is critical for driving operational efficiency. SKUBIQ’s integrates smoothly with various other enterprise systems, including ERP, TMS, and CRM systems, enabling a unified approach to managing logistics.
This seamless integration allows for the automatic exchange of information between systems, ensuring that all data is synchronized and reducing the need for manual data entry. The result is improved data accuracy, better decision-making, and a more agile logistics operation.
7. Advanced Reporting and Analytics
Data is only useful if you can extract actionable insights from it. SKUBIQ’s includes robust reporting and analytics features that provide businesses with detailed performance reports and key performance indicators (KPIs). These insights allow logistics managers to make informed decisions that drive continuous improvement in warehouse operations, order fulfillment, and inventory management.
By analyzing patterns and trends, companies can identify areas of improvement, reduce inefficiencies, and enhance customer satisfaction.
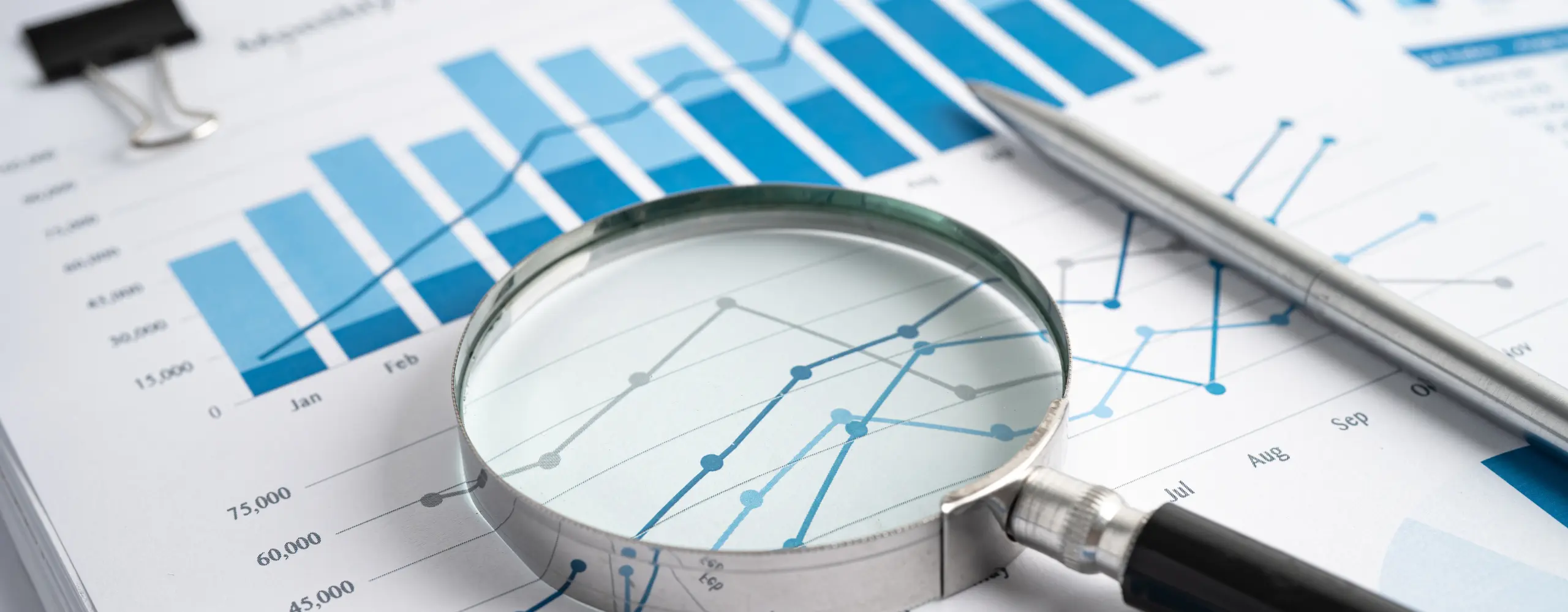
Achieving Operational Excellence with SKUBIQ
Driving operational excellence in in-plant logistics requires the integration of advanced technology, strategic planning, and data-driven decision-making. By improving real-time visibility, inventory accuracy, labor management, and system integration, SKUBIQ empowers businesses to achieve operational excellence and maintain a competitive edge in today’s fast-paced market.
For businesses looking to optimize their in-plant logistics operations and achieve greater efficiency, adopting SKUBIQ’s is a game-changing move that can result in substantial improvements across all facets of warehouse management.