Effective warehouse management system is crucial for the smooth functioning of any business’s logistics & supply chain management. Among the various processes within a warehouse, the inbound process holds a significant role. It involves the reception, inspection, and storage of incoming goods. Optimizing this process is essential for enhancing efficiency, reducing errors, and ensuring customer satisfaction. In this comprehensive guide, we will walk through the steps to streamline and enhance your inbound process in the warehouse.
Understanding the Importance of the Inbound Process in Warehouse
Before delving into the optimization steps, it’s vital to grasp the importance of the inbound process in the broader scope of warehouse management. The warehouse serves as the central hub for storing and distributing products, making the inbound process the starting point of the entire supply chain.
1. Receiving
The initial step involves the physical acceptance of goods. This phase is critical, as inaccuracies in counting or damage assessments can lead to downstream issues.
2. Inspection
Following receipt, a thorough inspection of the goods is essential. This step ensures that the received products meet the specified quality standards.
3. Storage
Proper placement of goods within the warehouse is crucial for efficient retrieval and subsequent order fulfillment.
Step 1: Implement a Robust Warehouse Management System (WMS)
To initiate the optimization process, invest in a state-of-the-art Warehouse Management System (WMS). This technology acts as the backbone of efficient logistics & supply chain management by automating and orchestrating various warehouse processes. A WMS helps in real-time tracking of inventory, improves order accuracy, and enhances overall visibility into the warehouse operations.
Step 2: Streamline Receiving Procedures
Efficient receiving procedures are fundamental for a successful inbound process. Implement the following steps to streamline this phase:
- Advanced Shipping Notifications (ASNs): Encourage suppliers to provide ASNs, allowing your system to anticipate incoming shipments, reducing the time goods spend in the receiving area.
- Cross-Docking: Evaluate the feasibility of implementing cross-docking, where goods are directly transferred from receiving to outbound shipping, bypassing storage. This minimizes storage costs and expedites order fulfillment.
Step 3: Enhance Inspection Processes
Accurate inspection is pivotal to maintaining product quality. Implement the following strategies:
- Quality Control Checkpoints: Establish dedicated checkpoints for quality control inspections. This ensures that each product undergoes a thorough examination before being accepted into inventory.
- Automated Inspection Technologies: Integrate automated technologies, such as barcode scanners and RFID systems, to enhance the speed and accuracy of inspections.
Step 4: Optimize Storage Strategies
Efficient storage directly impacts order fulfillment and overall warehouse operations. Consider the following to enhance storage processes:
- ABC Analysis: Categorize products based on their importance and frequency of movement. This allows for strategic placement, with high-demand items positioned for quick accessibility.
- Dynamic Slotting: Regularly reassess and reorganize storage locations based on product demand patterns. Dynamic slotting ensures that frequently picked items are conveniently located for efficient retrieval.
Step 5: Implement Cross-Functional Collaboration
Effective collaboration between different departments within the warehouse is crucial. Break down silos and encourage communication between the inbound process team, quality control, and inventory management teams. Cross-functional collaboration fosters a holistic approach to warehouse management, addressing issues promptly and preventing bottlenecks.
Step 6: Leverage Data Analytics for Continuous Improvement
Utilize data analytics tools to gain insights into the performance of your inbound process. Monitor key performance indicators (KPIs) such as receiving time, inspection accuracy, and storage efficiency. Analyzing this data enables you to identify areas for improvement and implement changes for continuous optimization.
Step 7: Prioritize Employee Training and Safety
Invest in comprehensive training programs for warehouse staff involved in the inbound process. Well-trained employees contribute to smoother operations and fewer errors. Additionally, prioritize safety protocols to create a secure working environment, reducing the risk of accidents and ensuring the well-being of your workforce.
Conclusion: Achieving Excellence in Inbound Process in Warehouse
In conclusion, optimizing the inbound process in warehouse is essential for achieving operational excellence in logistics & supply chain management. By implementing a robust Warehouse Management System (WMS), streamlining receiving procedures, enhancing inspection processes, optimizing storage strategies, promoting cross-functional collaboration, leveraging data analytics, and prioritizing employee training and safety, businesses can create a foundation for efficient and error-free warehouse operations.
Continuous improvement is key to staying ahead in the dynamic landscape of logistics & supply chain management. Regularly assess and refine your inbound process to adapt to changing business needs and technological advancements, ensuring that your warehouse remains a competitive asset in the broader supply chain.
Recent Blogs
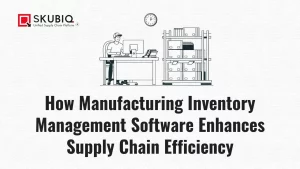
How Manufacturing Inventory Management Software Enhances Supply Chain Efficiency
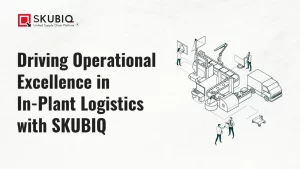
Driving Operational Excellence in In-Plant Logistics with SKUBIQ
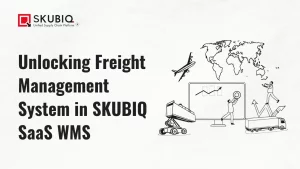